Drawbacks with
the Current Design
While
the use of LEDs, and the use of the LM334Z are
highly suited to what we are doing, they are not
the perfect solution. If we were living in a
perfect world the light would start to shine at 0.1V,
as it is it starts lighting at around 3V. It
reaches its brightest at just over 4V, which is
enough for many locomotives to be moving along
the track.
Another
issue I have found is the occasional flickering
of the reverse light. This is an issue with any
directional lighting system.
Voltage
Loss, Causes and Solutions
The
reason that the LED does not immediately light is
because there is voltage loss in the circuit.
LEDs use a PN junction, which just means it uses
one kind of semiconductor butted up against
another. Inherent in this junction is a voltage
drop. This means that the junction will not allow
the electricity to go through until it is over a
certain voltage. It will then typically "short"
all voltage past this point. For a typical diode
used for signal processing or rectifying the
voltage drop is around 0.5V. This would be grand,
but for our LEDs (which are just a special kind
of diode, a Light-Emitting-Diode) the voltage
drop is much higher. The voltage drop across an
LED relates to the frequency the LED has to
generate. The lower the frequency the lower the
voltage drop. This means that a Red LED has a
voltage drop of around 1.7 volts, and a Blue LED
has a voltage drop around 3.5V. I believe the
white LEDs which we find so valuable use an
ultraviolet frequency, then converting this to
visible light with a mix of florescent dyes. This
is much like the fluorescent tubes found in
lighting. This is unfortunate for us as it means
the frequency is even higher, giving us a voltage
drop of around 4V. Actually all those rated
voltage drops are slightly lower, but it takes a
little above the actual voltage drop to
illuminate the LED properly.
The
solution? Well, under most scenarios this is not
a real issue. I mean, we have immensely improved
the lighting performance already. If we want to
improve it further, we really have two options.
We could either artificially raise the voltage
experienced by the LED so that it will light
sooner, or we could artificially lower the
voltage the motor experiences, so that it moves
off slightly later. It is much easier to take
voltage away, rather than give extra, so we will
look at the second option first.
The
disadvantage to dropping the voltage the motor
experiences is that the locomotive will no longer
reach the same top speed. Usually this should not
be a problem, as few people crank their
locomotive up to full blast anyway. In order to
lower the voltage to the motor we can simply use
a semiconductor to our advantage. If we put two
diodes (facing opposite ways) inline with the
motor then the motor will experience a voltage
drop of around 0.5-0.6V. We can just use common 1N4004
power diodes, available from any electronics
store.
The
other option is to raise the voltage. While this
will preserve the locomotive's top speed, it is
more difficult to implement. This would nominally
involve some kind of voltage doubler. This would
be space permitting, as the unit would take up
around 1cm3 at a minimum. I offer the
following simple circuit, although I have not
finalised the designed, nor have I done testing
on it yet.
Voltage
Doubler Schematic
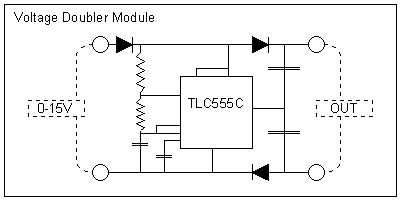
Reverse
Light Flickering, Causes and Solutions
The
reverse light flickering is caused by poor track
contact. It is really caused by the motor when
the power is instantaneously disconnected. This
is due to back EMF (electromotive force). To
understand this you must first understand that
current through a wire generates a magnetic field,
and a changing magnetic field generates a current
through a wire. The coils in the motor are really
a series of very long pieces of wire, and the
current generates the magnetic field the motor
uses to turn. If a coil is receiving a current,
and the current is disconnected, then the
magnetic field collapses. This collapsing
magnetic field constitutes a changing magnetic
field, and generates a reverse voltage in the
coil (this is called back EMF). In a motor this
would normally be offset by the changing magnetic
field that occurs as the coil moves past the
fixed magnet(s) in the motor, but not always (depending
on the position of the coil when the power fails).
Therefore we occasionally, when the power fails
and the coil is in a certain position, get a
reverse voltage applied to the circuit. This
reverse voltage is enough to ever so briefly
light the reverse light.
This
occurrence is common to any directional lighting
system (although it will be more apparent in ours
due to its high efficiency and speed), and cures
are usually easy. Firstly cleaning the track and
wheels of the locomotive should fix the problem
99%. If it does not, then a small capacitor
across the motor in the locomotive will provide a
permanent fix. The capacitor does not have to be
big, say a 0.047uF to 0.1 uF polyester capacitor
(often called a "Greencap"). These are
small and should be able to be tucked against the
motor somewhere.
|